亜鉛メッキとは?特徴や処理方法をご紹介

亜鉛メッキとは、鉄や鋼などの金属素材の表面に亜鉛をコーティングすることで、腐食やサビから保護する表面処理技術です。
機械部品や建築資材、日用品に至るまで、あらゆる製造業の現場で活用されており、コストパフォーマンスにも優れています。
特に製造現場では、製品の寿命や外観品質を大きく左右するため、設計段階から適切なメッキの選定が重要視されています。
この記事では、亜鉛メッキの基本知識から代表的な種類・特徴、処理方法、そして依頼時のポイントまでを、技術部門や設計担当者の方に向けてわかりやすく解説いたします。
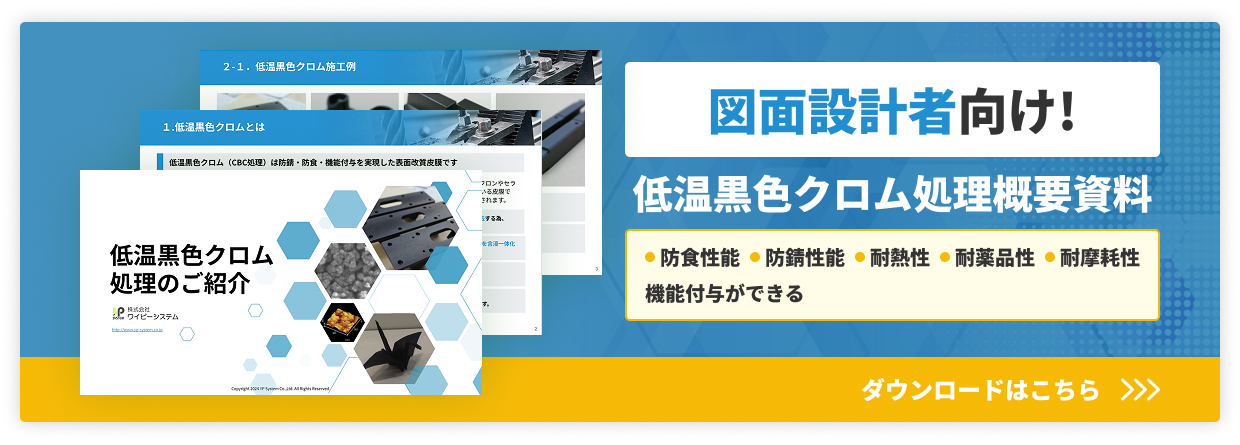
亜鉛メッキとは
亜鉛メッキとは、主に鉄や鋼といった金属材料の表面に、亜鉛の薄い層をコーティングする表面処理技術です。
酸化や腐食から素材を保護する、代表的な表面処理技術の一つです。
鉄素材は空気中や湿度の高い環境で酸化しやすく、サビの発生につながりますが、亜鉛を表面に施すことで酸素や水分との接触を遮断し、防錆性を大きく向上させることができます。
さらに、万が一、亜鉛層にキズがついた場合でも、鉄よりもイオン化傾向の大きな亜鉛が優先的に腐食するため、亜鉛自体が「犠牲防食作用」を発揮し、鉄が直接腐食するのを防いでくれるため、実用性の高い処理法として多くの産業で採用されています。
特に屋外で使用される構造材や、自動車部品、電子機器のシャーシなど、さまざまな製品に利用されています。
亜鉛メッキには、「電気亜鉛メッキ」と「溶融亜鉛メッキ」の2種類があります。
電気亜鉛メッキ
電気亜鉛メッキ(電解亜鉛メッキ)は、電気分解の原理を利用して金属表面に亜鉛を析出させる処理法です。
処理液(メッキ浴)の中で亜鉛を陽極にして、素材に陰極の電流を流すことで、素材表面に金属亜鉛の被膜を形成します。
電気亜鉛めっきは、溶融亜鉛めっきと比べ膜厚の制御がしやすく、外観の仕上がりが美しいという特長があり、自動車、精密機械部品など、外観品質が求められる分野で使用されることもあります。
ただし、溶融亜鉛めっきと比べ膜厚が薄いため、屋外用途や過酷な環境下での使用には適さないケースもあり、用途に応じた選定が必要です。
また、防錆性能を高めるために、メッキ後に「クロメート処理」が施されることがあり、光沢クロメートや黒色クロメートなど、仕上げのバリエーションも豊富です。
溶融亜鉛メッキ
溶融亜鉛メッキは、素材を高温(約450℃)の亜鉛槽に直接、浸すことで、素材表面に厚く強固な亜鉛被膜を形成する処理方法です。
「ドブづけめっき」「てんぷらめっき」と呼ばれることもあります。
表面に形成される亜鉛層は、鉄と亜鉛が合金化した層と純亜鉛層の2層構造となり、合金反応によって密着しています。
衝撃・摩擦により剥離することが、ほぼないため、非常に高い防錆性能を発揮します。
溶融亜鉛メッキは、橋梁や鉄塔、道路標識など、屋外で長期間使用される構造物や大型製品に多く採用されています。
メッキ層が厚く、耐久性が高いため、定期的なメンテナンスの手間を減らすことができ、ライフサイクルコストの面でも有利です。
ただし、処理温度が高い事や膜厚管理が容易でないため、精密部品や薄板製品には適さない場合もあります。
また、外観がやや粗くなることがあるため、美観重視の用途には向かないこともあります。
亜鉛メッキの特徴
亜鉛メッキは、その防錆性能の高さから多くの産業分野で活用されています。
特に、鉄鋼材料は腐食に弱いため、その保護手段として亜鉛メッキは非常に有効です。
ここでは、亜鉛メッキが持つ主要な特徴について解説します。
優れた防錆性能
亜鉛は空気や水に触れると酸化しやすく、酸化亜鉛の保護膜を形成します。
この保護膜が外部からの酸化因子を遮断することで、鉄素材が直接サビるのを防ぎます。
さらに、傷がついた部分でも「犠牲防食作用」により、亜鉛が先に腐食することで鉄を守ります。
均一な被膜形成と外観性
電気亜鉛メッキの場合、比較的、薄い被膜でも仕上げることができ、滑らかで美しい外観が得られます。
そのため、外観品質が求められる製品に最適です。但しクロメート処理が必要な場合は、ある程度の皮膜厚さが必要となります。
一方、溶融亜鉛メッキは厚いメッキ層により、より過酷な環境にも対応できる強靭さを備えています。
高い加工性と密着性
亜鉛メッキは、素材との密着性が高く、後工程での切断・曲げ加工にも対応しやすい特徴があります。
また、溶接や塗装との相性も良いため、複合的な加工を行う製造現場でも柔軟に対応可能です。
コストパフォーマンスに優れる
防錆処理としては比較的、安価でありながら、十分な性能を発揮できるため、コスト面でも非常にバランスが取れた技術といえます。
特に、量産品や構造材のように広範囲に防錆処理が必要な製品にとって、最適な選択肢の一つとなります。
環境対応の仕上げも可能
近年では、六価クロムを含まない環境配慮型の三価クロメート処理や、鉛フリーの溶融亜鉛メッキも登場しており、環境規制への対応が求められる用途にも対応可能です。
製品仕様書や顧客要望に応じた処理の選定が可能である点も魅力の一つです。
亜鉛メッキの処理方法
上記お伝えした通り、亜鉛メッキには、代表的な処理方式として、「電気亜鉛メッキ」と「溶融亜鉛メッキ」があります。
それぞれの工程には特徴があり、製品の仕上がりや性能にも大きく影響します。
以下に、各処理方法の工程を詳しく解説します。
前処理工程(共通)
亜鉛メッキにおいて最初に行われるのが「前処理」です。
この工程は、素材の表面に付着した油分・酸化物・汚れなどを除去し、メッキが密着しやすい状態に整えるために欠かせません。
主な工程は以下のとおりです。
脱脂 | 素材の表面に付いている油脂類などの汚れを除去するため、加温したアルカリ溶液に漬ける |
---|---|
水洗 | 脱脂液を洗い流す |
酸洗 | 塩酸または硫酸水溶液に漬け、素材の表面のさび、スケールなどの酸化物を除去し、鉄素地を露出させる |
水洗 | 残留薬品を洗い流す |
電解洗浄 | 本洗浄を目的としたり、酸洗を行った際に素材の表面に残ってしまったスマットを電気分解で除去 |
水洗 | 電解液を洗い流す |
この前処理の出来が、最終的なメッキ品質を大きく左右します。
電気亜鉛メッキの処理工程
電気亜鉛メッキは、以下のようなプロセスで行われます。
メッキ浴への投入 | 素材を電解液(ジンケート浴又はシアン浴)に浸ける |
---|---|
通電処理 | 素材を陰極、亜鉛板を陽極として電流を流すことで、素材表面に亜鉛を析出 |
水洗 | 電解液を洗い流す |
表面活性 | 硝酸溶液により亜鉛めっき表面の活性化処理を行う |
クロメート処理 (必要に応じて) |
防錆性や外観を向上させるための表面仕上げ |
水洗 | クロメート処理液を洗い流す |
乾燥 | 表面の乾燥を行う(エアブロー、熱風乾燥等) |
溶融亜鉛メッキの処理工程
溶融亜鉛メッキは、素材を高温の亜鉛槽に直接、浸ける方法です。
以下の工程を経て処理が行われます。
フラックス処理 | 酸洗い後、酸化防止と濡れ性向上のための薬品処理 |
---|---|
溶融亜鉛槽への浸漬 | 約450℃の亜鉛に数分間浸けて反応層を形成 |
冷却・仕上げ | 引き上げ後、表面を整えて冷却する |
処理方法の選定ポイント
処理方法の選定は、以下の点を考慮して判断する必要があります。
- 使用環境(屋内・屋外、湿度、腐食性)
- 外観の要件(美観重視か否か)
- 膜厚の希望(薄膜・厚膜)
- コスト/納期/加工性
たとえば、美観や精度を重視する場合は電気亜鉛メッキ、耐候性・長寿命を優先するなら溶融亜鉛メッキが適しています。
亜鉛メッキはその処理方法によって費用や性能・用途が大きく変わるため、製品設計時に最適な処理工程を選定することが非常に重要です。
詳細な処理対応や試作相談については、ワイピーシステムまでお気軽にご相談ください。
まとめ
亜鉛メッキは、防錆性や加工性、コスト面において非常にバランスの取れた表面処理技術です。
電気亜鉛メッキは外観品質に優れ、溶融亜鉛に比べ薄膜での均一な処理が求められる製品に最適である一方、溶融亜鉛メッキは厚膜による高い耐久性が求められる構造物や屋外部品に適しています。
どちらの処理方法にも明確な特長があり、製品の使用環境や設計要件に応じた選定が重要です。
また、いずれの処理方式でも、前処理や後処理を含む一連の工程が最終的な品質に大きく影響します。
したがって、信頼性の高い加工業者の選定も、長期的な製品性能を左右する大きなポイントです。
今後の製品開発や設計業務において、亜鉛メッキの特性と処理方法を正しく理解し、最適な選択をすることが、高品質なものづくりへの第一歩となります。
加工相談や処理方法の選定にお困りの際は、ぜひワイピーシステムまでお気軽にご連絡ください。