無電解ニッケルメッキとは?特徴・仕組みや用途を解説
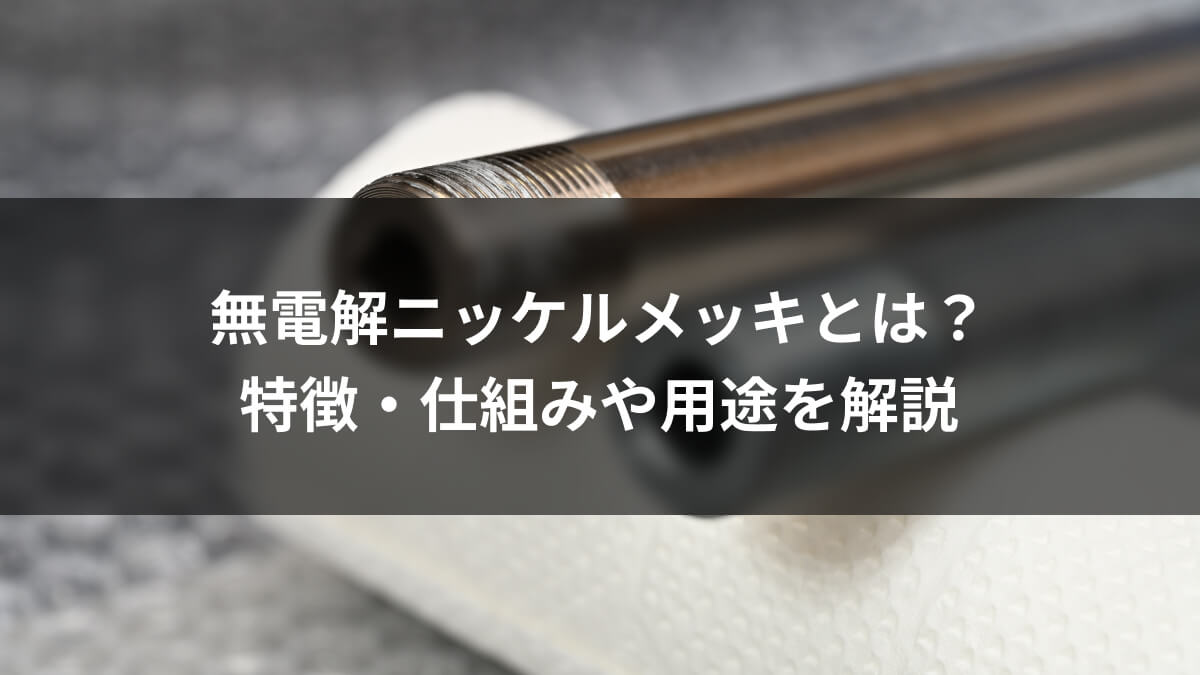
無電解ニッケルメッキとは、電気を使用せず、化学反応により金属表面にニッケルを析出させる表面処理技術です。
金属表面処理における重要な技術の一つであり、電子部品や精密機械など幅広い製品で採用されています。
近年、液晶・半導体・自動車・電子・医療機器といった分野で部品の小型化・高精度化が進む中、電気を使わず均一なメッキが可能な技術として注目されています。
この記事では、「無電解ニッケルメッキ」の基本的な仕組みや特徴、用途、そしてメリットとデメリットについて、製造業の設計・技術担当者にわかりやすくご紹介いたします。
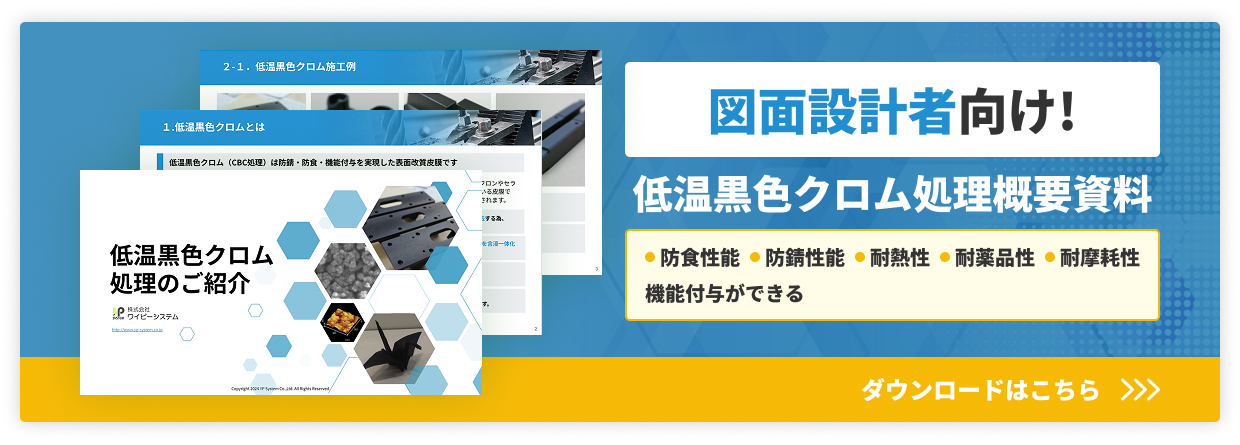
無電解ニッケルメッキとは
無電解ニッケルメッキとは、電気を使用せず、還元剤(一般的には次亜リン酸ナトリウムなど)を用いて、素材そのものを触媒とした化学還元反応により、金属表面にニッケルを析出させる表面処理技術です。
従来の電気ニッケルメッキとは異なり、電気を使用しないため、部品の形状や配置に左右されず、全体に均一な厚さのメッキ皮膜を形成できるのが大きな特長です。
このため、複雑な形状の部品や非導電性の素材にも均一なメッキを施すことが可能で、精密機器や高機能部品の製造現場で幅広く活用されています。
また、導電性を持たない樹脂やセラミックなどの素材にも処理が可能であり、用途の幅を大きく広げています。
電気ニッケルメッキとの違い
メッキでは、電気を使って素材の表面に金属の被膜を付ける方法が一般的です。
電気ニッケルメッキでは、素材及び電極板に電流を流し、電極反応を通じてニッケルイオンを陰極側(処理物)に析出させます。
このため、電気の流れや電極板からの距離、また流れる電流量や素材表面状態によって、膜厚にばらつきが生じやすく、形状が複雑な部品では不均一なメッキになりやすいという課題があります。
また、電気ニッケルメッキでは皮膜に対するニッケル含有割合は99%以上と高いですが、無電解ニッケルメッキの皮膜にはリンが含まれ、ニッケル含有割合が86~92%程度となります。
無電解ニッケルメッキの用途
無電解ニッケルメッキは、耐食性・耐摩耗性・はんだ付け性・導電性といった多様な機能を持つことから、以下のような多岐にわたる分野で活用されています。
- 自動車部品(エンジン関連部品、バルブ、シャフトなど)
- 電子機器(コネクタ、リードフレーム、プリント基板など)
- 医療機器(手術器具、インプラント部品など)
- 機械部品(ベアリング、油圧ポンプシリンダーなど)
- プラスチック製品の加飾・機能性付加(絶縁体へのメッキ)
そのほか、半導体業界や航空宇宙分野など、品質・精度が重視される先端産業でも不可欠な処理技術となっています。
無電解ニッケルメッキの特徴
無電解ニッケルメッキは、電気を使わない独自の処理方式により、従来の電気メッキとは異なる機能性と処理性の高さが特長です。
ここでは、設計・技術担当者が押さえておきたい主要な6つの特性について解説します。
耐食性が優秀
無電解ニッケルメッキは、均一な膜厚で被膜を形成できるため、隙間や凹凸のある表面でも高い耐食性能を発揮します。
特に、リンを含んだニッケル層は、化学的に安定しており、酸やアルカリ、塩分環境下でも腐食しにくいため、自動車部品や海洋構造物など過酷な環境下での利用にも適しています。
メッキ後の熱処理で硬度が向上
無電解ニッケルメッキは、熱処理を加えることでさらに硬度を高めることが可能です。
たとえば、リンを含むメッキでは、300~400℃の加熱処理によりニッケルリン合金中にNi-P(ニッケルリン化合物)相が形成され、硬度が700~1,000HVに達することもあります。
この処理により、耐摩耗性や耐久性が大幅に向上し、摺動部品などにも対応できます。
さまざまな粒子と複合させることで特性を獲得させることができる
無電解ニッケルメッキは、セラミック粒子やPTFE、ダイヤモンド粉末などを共析する「複合メッキ」にも対応可能です。
これにより、潤滑性・耐摩耗性・耐熱性・撥水性といった多機能性を追加することができるため、用途に応じたカスタムメッキとしても注目されています。
硬度が高い
無電解ニッケルメッキは、処理条件の最適化や熱処理により、セラミック並みの高硬度を持つ皮膜が得られるため、アルミ素材や樹脂素材に耐摩耗性を付加したい場面でも有効です。
※アルミ素材や樹脂素材の場合、熱膨張係数の違いから、めっきフクレ等が発生する可能 性があるため、注意が必要です。
絶縁体でもメッキ処理が可能
無電解方式の最大のメリットの一つが、電気を必要としないため絶縁体素材(樹脂、セラミック、ガラスなど)への処理が可能であることです。
このため、無電解ニッケルメッキも、絶縁体へのメッキ処理が可能です。
前処理で触媒を付けることで、導電性のない素材でも安定した析出反応が起き、装飾性と機能性の両立が図れます。
複雑な形状にも対応
化学反応によってメッキを施すため、穴・溝・内径部など、電気が届きにくい形状でも均一な被膜を形成できます。
これは、射出成形品や精密機械部品のように、複雑な幾何形状を持つ部品にとって非常に重要な特性です。
結果として、後加工の手間や品質リスクを低減できるというメリットがあります。
無電解ニッケルメッキの種類
無電解ニッケルメッキは、メッキ中に含まれるリン(P:phosphorus)の含有量によって主に3つのタイプに分類されます。
このリンの濃度によって、メッキ皮膜の特性や用途が大きく異なるため、目的に応じた適切な選択が必要です。
低リンタイプ
低リンタイプの無電解ニッケルメッキは、硬度と導電性に優れており、はんだ付け性にも良好な性能を示します。
皮膜は結晶性が高く、磁性を持ち、機械加工後の部品に対して摩耗耐性を付与したい場面で有効です。
また、高温環境でも皮膜が安定するため、エンジン周辺部品など高温にさらされる機械部品への適用に向いています。
ただし、耐食性に関しては他のタイプと比較して劣るため、腐食環境には不向きです。
■主な用途例
- 金属部品の機械的耐久性向上
- 電子部品の接点部処理
- 切削加工後の摩耗対策部品
中リンタイプ
中リンタイプは、硬度・耐食性・加工性のバランスが非常に良い「汎用型」の無電解ニッケルメッキです。
皮膜は微結晶またはアモルファス構造に近く、電磁特性や表面平滑性にも優れます。
そのため、幅広い産業分野で最も多く使用されているタイプであり、自動車部品・電子機器・精密機械など多くの製品に対応しています。
初めて無電解ニッケルメッキを採用する際の選択肢としても適しています。
■主な用途例
- 電子部品のリードフレーム
- 通常環境下の工業部品
- 表面平滑性が求められる機械部品
高リンタイプ
高リンタイプは、非常に高い耐食性と非磁性が特長です。
皮膜はほぼ完全なアモルファス構造で、化学的に安定しているため、酸性・アルカリ性の腐食性環境でも優れた耐久性を発揮します。
また、非磁性を活かして、磁気の影響を避けたい精密機器の外装部や電子機器部品にも適しています。
ただし、結晶構造を持たないため硬度は比較的低めですが、後工程で熱処理を施すことで硬度の向上も可能です。
■主な用途例
- 医療機器や半導体装置の部品
- 海洋・化学プラント部品
- 非磁性が求められる電子・光学機器
リン含有率により性質が変化する無電解ニッケルメッキは、設計者や技術者が最終製品の使用環境に応じて選択すべきです。
適切なメッキ種の選定が、製品の信頼性や長寿命化にも直結します。
無電解ニッケルと電解ニッケルを比較したときのメリット
表面処理技術として長年使われてきた電解ニッケルメッキに対し、無電解ニッケルメッキは電気を用いず化学反応でニッケルを析出させることで、多くの場面で代替または補完的な選択肢として注目されています。
「無電解ニッケルメッキの特徴」でご紹介した内容と重なる部分もありますが、ここで改めて
均一な膜厚が得られる
無電解ニッケルメッキの最大のメリットは、部品全体に均一な厚さのメッキ層を形成できる点です。
電解メッキでは電流が流れやすい部分(凸部や外周)に厚く析出し、内側や奥まった部分にはメッキが付きにくいため、膜厚のムラが生じやすい傾向があります。
しかし、無電解メッキは溶液中の化学反応のみで析出が進むため、複雑な形状や内径、細かい溝にも均一に皮膜を析出させることができます。
このため、寸法精度を厳しく求められる精密機器の加工工程において、仕上げ精度の安定化や加工省力化を図れます。
非導電性素材にも対応可能
電解メッキでは、素材が電気を通すことが前提であるため、樹脂・セラミック・ガラスなどの非導電体には直接メッキを施すことができません。
一方、無電解ニッケルメッキは化学的反応を用いてメッキ処理を行うため、非金属基材にも処理が可能です。
このため、プラスチック製品に装飾性や導電性、防錆機能を付与したい場合にも有効で、近年の軽量化ニーズやデザイン性を求める部品設計において欠かせない技術となっています。
耐食性・耐摩耗性に優れる
無電解ニッケルメッキは、リンを含む皮膜がアモルファス構造を形成しやすく、化学的に安定しているため、耐食性に優れています。
特に、高リンタイプの無電解ニッケルは、酸性や塩水環境に強く、過酷な条件下でも腐食を抑えることが可能です。
また、熱処理を加えることで高い硬度(700~1000HV)を得ることができ、耐摩耗性の向上にも寄与します。
これらの特性は、電解ニッケルメッキでは一部の特殊処理が必要となることが多く、無電解方式の方が効率的かつ安定的に実現できるとされています。
処理設備が比較的コンパクト
電解メッキには電源装置やアノードなどの設備が必要ですが、無電解メッキは薬液槽と加熱装置のみで処理が可能です。
そのため、省スペースな導入が可能であり、小規模な工場やパイロットラインにも適しています。
また、設備がシンプルな分、メンテナンス性も高く、ライン設計の柔軟性が確保できることも大きなメリットです。
無電解ニッケルと電解ニッケルを比較したときのデメリット
無電解ニッケルメッキには多くのメリットがある一方で、電解ニッケルメッキと比較した際のデメリットや注意点も存在します。
ここでは、主なデメリットをご紹介します。
メッキ液の管理が難しい
無電解ニッケルメッキは、化学反応によってメッキが進行するため、溶液の状態を常に安定に保つ必要があります。
リンやホウ素を含む還元剤は徐々に消費され、反応の進行に伴い副生成物も蓄積されていきます。
そのため、定期的な成分分析と補充、場合によっては液交換が必要になるという点で、運用管理の難易度は電解メッキよりも高めです。
生産コストがやや高い
無電解ニッケルメッキでは、薬剤が高価で、液管理に手間がかかるため、総じて処理コストが高くなる傾向があります。
電解メッキと比較し、同じ被膜厚を得るためにかかるコストは2~3倍程度になる場合もあり、大量生産品においてはコストインパクトが無視できない要素となります。
また、薬液の寿命も限られており、メッキ槽の維持管理にかかるコストや手間も含めてトータルコストとして評価することが求められます。
メッキ速度が遅い
無電解メッキは化学反応に依存しているため、処理速度は比較的遅めです。
一般的に、1時間あたりのメッキ厚は10~25μm程度であり、電解メッキのように短時間で厚膜を形成することは難しいため、大量処理や高スループットが求められる現場では処理時間がボトルネックになる可能性があります。
処理後の廃液処理が必要
無電解ニッケルメッキは、リン酸やホウ素などを含んだ化学薬品を使用するため、廃液処理の対応が必須となります。
環境への配慮から、処理後の薬液は法令に基づき適切に処分しなければならず、産業廃棄物としての取り扱いコストや安全管理の手間も必要です。
特に環境負荷を軽減したい企業では、廃液処理の設備投資や外部委託先の選定など、事前の検討が重要になります。
まとめ
無電解ニッケルメッキは、電気を使用せず化学反応によって金属表面にニッケルを析出させる先進的な表面処理技術です。
複雑な形状や非導電体にも対応できる加工性の高さ、均一な膜厚、高い耐食性と耐摩耗性といった特長から、電子部品、自動車、医療機器などさまざまな製品分野で活用が進んでいます。
また、リン含有量によって性質の異なる「低リン」「中リン」「高リン」の各種タイプがあり、用途に応じた柔軟な選定が可能です。
電解ニッケルメッキに比べて高性能な一方で、液管理の複雑さやコスト面での課題も存在するため、導入には総合的な判断が求められます。
設計段階から製品の耐久性や信頼性を高めるために、最適な表面処理を選定することは製品品質の鍵を握る要素です。
自社製品におけるメッキ処理の見直しや改善を検討する際には、無電解ニッケルメッキの特性と適用可能性を踏まえた評価を行うことが重要です。
無電解ニッケルメッキに関するご相談は、ぜひワイピーシステムまでお気軽にご連絡ください。